Spinning process pdf
- PDF Novel Plasticized Melt Spinning Process of Polyacrylonitrile Fibers.
- PDF Airjet Spinning of Cotton Yarns - Cotton Incorporated.
- Gel spinning process pdf - FREE SPINS NO DEPOSIT MOBILE CASINO.
- Melt Spinning , Dry spinning and Wet Spinning Method.
- Metal Sheet Spinning process | Sheetmetal Forming.
- PDF Analysis of tube spinning process.
- Metal Spinning 101: A Complete Guide.
- Metal spinning - Wikipedia.
- Metal Spinning- Design Consideration and parameter of spinning.
- Spinning Process - Textile Spinning Process Flow Step by Step.
- PDF Spinning process optimization and microstructure of.
- US5393477A - Air gap spinning process for aramids - Google Patents.
- Metal forming: an analysis of spinning processes | Request PDF.
- Introduction to Spinning Process - Online Clothing Study.
PDF Novel Plasticized Melt Spinning Process of Polyacrylonitrile Fibers.
Introduction of spinning process Spinning is a manufacturing process for creating polymer fibres. There are many types of spinning: wet, dry, melt, gel, and electrospinning. It is a specialized form of extrusion that uses a spinneret to form multiple continuous filaments. 7. Types of spinning process Melt spinning Dry spinning Wet spinning 8. Metal spinning, also known as spin forming or spinning or metal turning most commonly, is a metalworking process by which a disc or tube of metal is rotated at high speed and formed into an axially symmetric part. Spinning can be performed by hand or by a CNC lathe.. The metal spinning trade is one that dates back to antiquity and was a skill used in the Ancient Egyptian era. May 01, 2022 PDF | Defects, such as cracks, typically occur in the spinning process of ternary catalyst shells.... Metal spinning process is widely used because of its low power requirement to producing.
PDF Airjet Spinning of Cotton Yarns - Cotton Incorporated.
Shear spinning is a process related to conventional spinning and is also known as flow turning or spin forging. In a conventional spinning operation the work is essentially formed by bending. There is usually not much change in the thickness of the sheet metal. The diameter of the work in conventional spinning must be large enough to account. Spinning techniques that are practiced: manual conventional spinning Ref 1, 2, power spin-ning Ref 411, and tube spinning Ref 7, 8. The first two of these techniques are described in this article. Tube-spinning technology is de-scribed in the articles Flow Forming and Roll Forming of Axially Symmetric Components. The scheme of the multi-step spinning process for manufacturing the large disc-like part with thin web and thick rim is shown in Fig. 2, in which the tool set-up and the geometrical shape of the, as well as the groove of the final roller are illustrated.From Fig. 2a, a workpiece is clamped between the upper die and lower die and all of them rotate together.
Gel spinning process pdf - FREE SPINS NO DEPOSIT MOBILE CASINO.
The main advantage of the SiroSPUNTM process is a reduction in spinning costs for pure fine wool weaving yarn. On average, SiroSPUNTM technology lowers the processing costs of spinning by 56 per cent. Weaving yarns are normally two-fold - that is, made up of two yarns twisted together. Ordinarily the strands must be first spun and then..
Melt Spinning , Dry spinning and Wet Spinning Method.
In a spinning process, a viscous polymer solution is extruded through the small size annulus of a spinneret. It is subjected to shear stress even though the traversing time of a polymeric dope solution is normally short as it involves only a few millimeters in the annulus. Other researchers have investigated and ascertained that the.
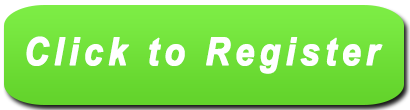
Metal Sheet Spinning process | Sheetmetal Forming.
Open-End Spinning The heart of the open-end process is a rotor see Exhibit 3, wherein fibers can be collected and then drawn off as a yarn. For short staple spinning, most rotors are 31 to 56 millimeters in diameter and may contain a shallow quot;Uquot; or quot;Vquot; shaped fiber alignment groove around their periphery. In open. Fig.1: Traditional type spinning lathe with T-rest 2.2.Process variables Although conventional spinning is different from shear and flow forming in terms of deformation characteristics, the set of process variables governing conventional spinning also determines the qualities of a shear or flow formed product. There are.
PDF Analysis of tube spinning process.
The MVS spinning frame has core-spinning capability. This is a process in which a filament or staple yarn is fed behind the front roll of the drafting system and covered or wrapped with another fiber during the spinning process. Figure 3 shows the composition of a core spun yarn. Figure 3. Core Spun MVS Yarn Courtesy of Muratec Covering fibers.
Metal Spinning 101: A Complete Guide.
Yarn that has been produced in spinning mill will be sent to the Knitting or Weaving factory. Here, fabric will be produced and send to the garments factory for garment production. Objectives: A spinning mill is space consuming industry. From raw cotton to yarn processing, lot of machineries are involved. Spinning is the process of manufacturing yarn from fiber during ring yarn manufacturing various machines are involved for the production namely Blow room, Carding, Comber, Draw frame, Speed Frame and Ring frame. Calculations plays very crucial role during the of yarn. Some important spinning production calculations are mentioned in the following specially about spinning production formula. Steps in Spinning Process. Step 1Metal Forming. This step involves the laying down of the material onto the mandrel. It is accomplished with short inside to outside moves.Material gets easier to form as the part is closer to completion. Steps In Sheet Metal Forming Process. Step 2Trimming. Parts having been spun are trimmed at the end to.
Metal spinning - Wikipedia.
Spinning is the process of taking textile fibers and filaments and making them into yarn. For thousands of years, people spun natural fibers into yarn by hand. Today, spinning involves many. Spinning process is an initial step to produce textile layout such as garments, fabric, home textile and so on. People used to convert fibers into yarn i.e. the spinning process by hand before a couple of decades which has now been mostly replaced by advanced technology of mechanical spinning carried in textile mills.
Metal Spinning- Design Consideration and parameter of spinning.
3.6.1 Melt spinning. Melt spinning is a manufacturing process used to produce synthetic fibers. This method can be used to create fibers for fabrics or to spin glass into fine threads for fiberglass production. It utilizes a rapid cooling system to transform melted base materials into long strands or filaments. Viscose rayon can be found in cotton-like end uses as well as silk-like end uses. Viscose rayon is the oldest commercial man-made fiber. It is naturally regenerated cellulosic based material such as wood pulp, cotton, linters. etc the degree of polymerization is 400 to 700 and the chemical structure of viscose resembles to cotton to be specific cellulose. A Straightforward Text Summarizing All Aspects of Process ControlTextile manufacturing is one of the largest industries in the world, second only to agriculture. Spinning covers a prominent segment in textile manufacturing, and this budding industry continues to thrive and grow. Process Management in Spinning considers aspect of process management, and offers insight into the process control.
Spinning Process - Textile Spinning Process Flow Step by Step.
The most common measuring method to characterise the dynamic yarn path in the ring spinning process is to measure the yarn tension, where the yarn path is almost straight. However, it is much more complex to measure the yarn tension at the other positions, for example, between the yarn guide and traveller balloon zone and between the traveller and winding point of the cop winding zone, as.
PDF Spinning process optimization and microstructure of.
Production spinning route for synthetic fibres, is also used to process wool for carpet yarns. There are a number of processes common to both systems: blending of the wool types to be used; scouring of the wool to remove a range of impurities e.g. dirt and grease; carding to. The structural changes during melt spinning process of polyethylene, polypropylene and polybutene-1 were studied making use of direct measurements. A model spinning apparatus was devised for this purpose. Measurements of diameter, birefringence and surface temperature were carried out. Wide and small angle x-ray photographs were taken at the successive points below the spinneret, moreover, the.
US5393477A - Air gap spinning process for aramids - Google Patents.
Repeat. Hot spinning heats a flowformed metal tube as it spins on a lathe at high speeds while various rollers and tools shape the piece. Computers control various machine tools that adjust for everything from feed rate, coordination, location, temperature and speed. The process accurately controls the profile of the neck while delivering.
Metal forming: an analysis of spinning processes | Request PDF.
Here, the spinning process is considered as a plane strain process, and the deformations are expressed by the diameter of the workpiece, and the spinnability is evaluated by the forming limit.
Introduction to Spinning Process - Online Clothing Study.
Mar 23, 2019 Introduction to Spinning Process. Spinning is the process of conversion of textile fibers and filaments into yarns for weaving or knitting into fabrics. In this article, we are going to know about the various processes which lead to the formation of worsted spun yarns. Worsted spun yarns differ from the regular woollen yarn in various properties..
Other links:
Heart Of Vegas Slots Free Play